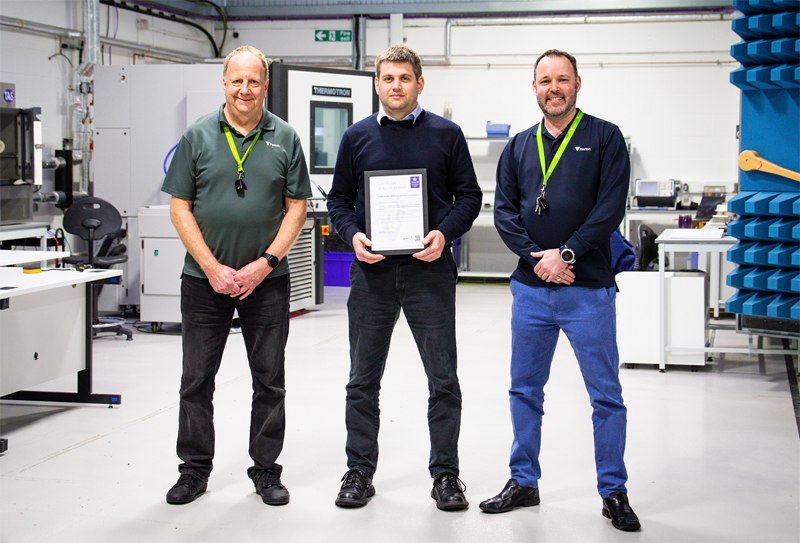
Paxton’s test facility team
Paxton has gained UKAS accreditation for its in-house public-facing product test facility.
UKAS visited Paxton’s UK headquarters in Brighton to carry out a formal assessment of EMC Test Facility which originally opened in August 2019. The government-appointed agency assessed Paxton’s ability and competence in performing product testing including an audit of the quality management system. The facility has now been officially granted UKAS accreditation, confirming that it meets the ISO 17025 standard for Laboratory Accreditation.
Brett Glass, Paxton’s Compliance Manager has overseen the development of the facility. He explains: “We are extremely proud to have gained UKAS accreditation. For any manufacturer looking for the highest possible quality and level of testing, this is the accreditation they want and need. Gaining it has been an in-depth and worthwhile process. Our Compliance team has been working towards it for some time whilst testing our products and that of many manufacturers from the South East of the UK.”
Paxton opened the test facility to maximise the efficiency and quality of its own product development. It has enabled them to launch new products and system additions quickly during the pandemic and global component shortage.
Whilst researching during the planning phase of the facility, Paxton decided to offer product testing externally to support businesses with quick pre-compliance testing and a bespoke service. The facility includes an Electromagnetic Compatibility Chamber (EMC) for manufacturers who need to perform emission and immunity tests at three metres. It also has equipment to carry out Electrostatic Discharge (ESD), surge, transients, and power quality tests.